Dortmunder Brauereien place multi-million order with KHS Group
News General news
- Bottlers record rising demand for beverage cans
- KHS filling line impresses with efficiency and cost-effectiveness
- Machine processes up to 80,000 cans per hour
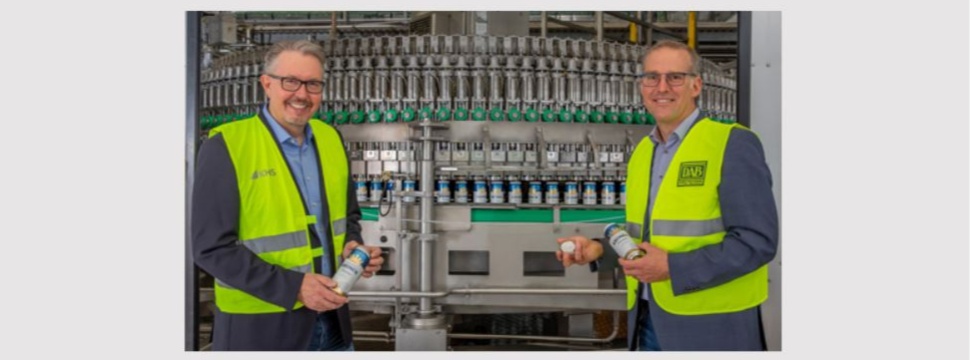
Despite the Corona crisis, Dortmunder Brauereien is investing in a new, ultra-modern and particularly resource-saving filling line for beverage cans. The multi-million order goes to the KHS Group, which is also based in the Ruhr metropolis - a forward-looking signal for Dortmund as a business location.
Brinkhoff's, Dortmunder Kronen, or DAB: what is brewed on Steigerstrasse according to traditional recipes and is left to mature in the cool fermenting cellar is then filled into various containers: the majority in returnable bottles, a not inconsiderable proportion in kegs for the catering trade, but the beverage can is also once again playing a more important role in the filling plans of the Dortmunder Brauereien - for sale in Germany, but above all for a growing export business.
Lion's share in returnable packaging
"Even if returnable packaging continues to account for the lion's share at our breweries: Trade customers and consumers are increasingly asking for beverage cans again since there has been a nationwide return system with deposit machines," says Uwe Helmich, Managing Director of Dortmunder Brauereien. A look at the industry statistics confirms this trend: more than four billion cans are likely to have been sold nationwide in 2020, filled with beer, soft drinks and more. Ten years earlier, the volume was still around 980 million units.
Three percent packaging and 97 percent product
Brinkhoff's No.1 and Dortmunder Kronen Pilsener are now not the only beers available in cans. The Dortmund breweries offer DAB Export in particular in this form of packaging. For good reasons, as Managing Director Uwe Helmich knows: "Little packaging, high light protection, and a good transport balance are plus points, especially in the export business: so when our DAB Export sets off overseas in cans, of 100 percent total weight, only three percent is packaging and 97 percent is product." By way of comparison, while a standard empty 0.5-liter bottle weighs around 365 grams, a beverage can weighs only around 12 grams. When the first beer can was launched on the market in 1935, it weighed around 100 grams.
The lighter the modern beverage can is today, the more sophisticated the line has to be on which it is filled tens of thousands of times every hour. As one of the leading manufacturers of filling and packaging systems in the beverage industry, the Dortmund-based KHS Group specializes in this.
"As a market leader in this sector, the idea of sustainability always plays an important role in the development of innovative and economical products," explains Dirk Dünnhaupt, KHS sales manager for North Rhine-Westphalia. "For the Dortmunder Brauereien, for example, we've designed a state-of-the-art system that will save around 50 percent electricity and 65 percent water compared to the predecessor model currently still in operation." By way of comparison, these savings would enable around 215 four-person households to cover their entire electricity requirements for a year, and in terms of water consumption, the figure is still 20 households of the same size.
Short distances facilitate project planning
In addition to the high technological standards and cost-effectiveness of the new filling line and its economical use of valuable resources, the local proximity and short distances between the Dortmunder Brauereien and KHS were also decisive factors in the awarding of the contract.
Planning for the conversion work on Steigerstrasse is already in full swing. As early as this summer the system, which weighs several tons, is to be delivered in individual parts, brought in, and assembled on site so that it can then be integrated into the production process during ongoing operation. An enormous challenge for the teams from the Dortmunder Brauereien and KHS which, according to current plans, should be completed by November.
The aim is for up to 80,000 cans per hour to pass through the new filling line by the end of the year. Steffen Krauß says, "Lines of this size always mean an investment in the high single-digit millions. The fact that we are able to handle this during the Corona crisis is a clear signal of the future viability of our site," says the head of plant engineering. And Uwe Helmich adds: "This investment underlines our important function as a hub for the can business of our group of companies in Germany and abroad - and that also makes us a little proud."