Modernisation instead of standstill
News General news
Brauerei Gold Ochsen secures additional flexibility in keg filling with new filling line and sets new standards in terms of efficiency
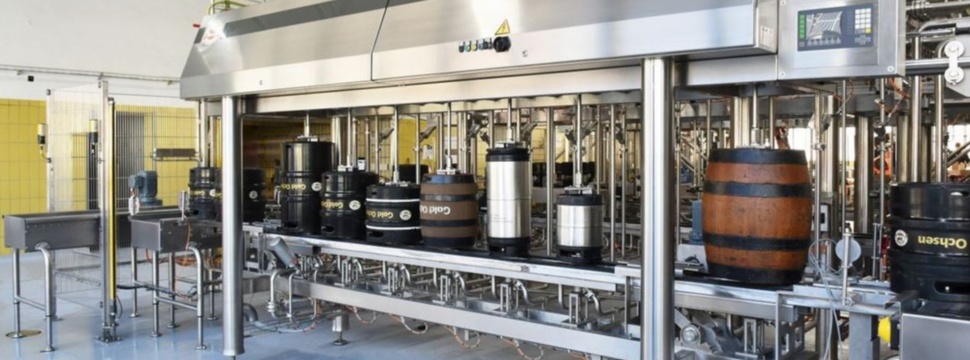
In June, a new cask filling line went into operation at the Gold Ochsen brewery, with which the traditional Ulm-based company is setting the course for the future. The plant, which is considered one of the most modern of its kind in southern Germany, now also allows beer to be filled in so-called slim kegs. Instead of the previous 30- and 50-litre kegs, smaller containers with 10, 15 and 20-litre capacities can now be filled for the first time. At the same time, the new line with an output of 300 units per hour plays to its strengths with the non-alcoholic soft drinks produced under the umbrella of the Gold Ochsen brewery. Where previously two filling lines were used for beer and soft drinks, one system now takes over that can be converted for the respective purpose in a very short time. In this way, on the one hand, the aspect of sustainability is specifically taken into account, but also the process optimisation in production is further advanced. The multi-talent, which corresponds to the latest state of the art, was launched by Managing Director Ulrike Freund herself.
Thanks to this further milestone in the history of the Gold Ochsen brewery, completely new scope is opening up in customer delivery. "We can now also supply our gastronomy partners with smaller units of draught beer and thus react much more flexibly to individual needs. Especially in the current situation, this is a decisive advantage. After all, it is currently not clear to all of us how the demand situation on the part of the gastronomy sector will develop in the future. But even beyond that, we see the 50-litre keg more as an opportunity for large event functions, which will soon be back to normal." Ulrike Freund remains optimistic.
Modern processes ensure sustainability
How high the potential of the new system is in the context of the brewery's internal processes will become apparent in the coming weeks. The advantages in terms of space savings and shorter distances, as well as less effort for maintenance and service by concentrating on just one plant, are already obvious. In addition, the conversion will have a positive effect on operating costs. "In our eyes, the modernisation of our bottling comes at the right time not only in spite of Corona, but precisely because of it," says Ulrike Freund. "Of course, we would have preferred a different starting situation, but this way we can also demonstrate once again that we are not burying our heads in the sand and firmly believe in the future after the pandemic," says the managing director combatively.
From plan to reality in the midst of the pandemic
The project, which involves an investment of 3.9 million euros, was already planned in 2019. In February 2020, shortly before the outbreak of the pandemic, the tender was issued, which was initially stalled by the first lockdown. Then, in June, the nails were put in the coffin and the reconstruction began.
State-of-the-art technology
The contract for the implementation was awarded to two companies from the region. The technology for the cleaning and filling stations comes from Albert Frey AG from Wald in Allgäu, a specialist in plant engineering and a well-known name in the brewing industry. "The performance characteristics and relevant references were simply convincing," says Stephan Verdi, 1st brewmaster and technical operations manager at Gold Ochsen. With the ultra-modern functions in the context of quality assurance, on which many renowned German large breweries also rely, the traditional brewery in Ulm can pay tribute to its high standards in beer production all along the line, as Verdi explains with an example: "Sophisticated residual pressure detection and multiple test runs mean that defective barrels are sorted out immediately. The system also meets the highest standards in terms of cleaning, load securing and energy efficiency." Augenstein Maschinenbau GmbH from Günzburg was the second project partner responsible for setting up the palletising system and further optimising the process chain. The company was the only supplier who could realise the vertical conveyor for transporting the barrels between the different floors in the existing lift shaft.